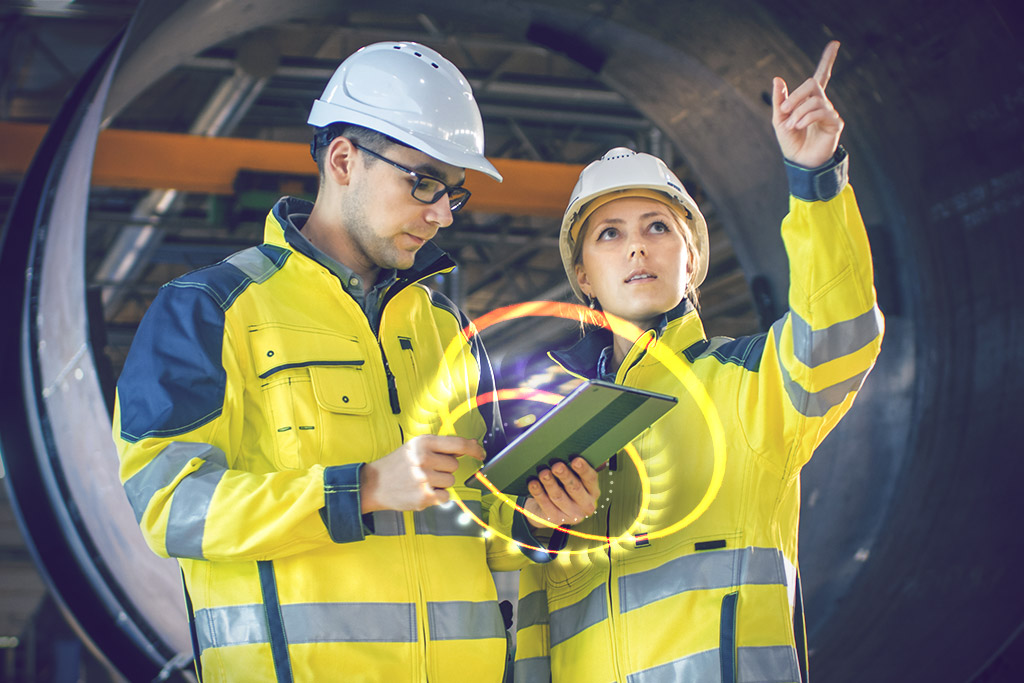
Technology and manufacturing have always gone hand in hand. Over the past decade, the concepts of Digital Manufacturing and Industry 4.0 — the fourth Industrial Revolution, as they call it — have framed a new battleground for the implementation of digital technologies in the industry. At a high-level, this industry transformation not only implies leaving the old paradigm of company-provides-goods-to-clients, but also calls for a more consumer-centric, responsive and agile type of production.
While many companies focus on the latest modern equipment and achieving connectivity of their industrial machine by IoT, the real challenge lies in leveraging new types of information, building new types of business relationships, and finding new ways of growth and scalability for the companies. Here are some of the digital trends that are currently changing the landscape of the manufacturing industry, and a quick overview of the potential behind them.
1. In production, the consumer should come first
In the old model of the manufacturing industry, companies produced standardized goods to an identified and willing-to-pay market. These days, however, seem to be quite the opposite: thanks to the Internet, audiences are actively demanding and funding products and services they want. Group funding services like Kickstarter and Indiegogo have revealed the will of the consumer to support new products and services on a smaller scale, and Etsy and Amazon Handmade nurture the market for handcrafted and custom goods.
While standardized goods are needed to achieve efficiency in manufacturing through high volumes of production, the challenges of how to become a manufacturing consumer-centric company are quite real. Levi’s online Tailor Shop is a clear example of diversification where the company can offer both their signature goods and showcase their ability to understand and customize what they produce to fit (literally) their market.
2. No longer a straight line: business as a digital environment
Any company that deals with producing consumer goods can understand the "ins and outs” of dealing with multiple other companies in the form of providers, suppliers, buyers, or overall maintenance. This is typically represented as a single line that goes from farm to market or from sea to kitchens in restaurants — each company or business involved in the process deals with their specific step of production.
Digital technology has changed our way of understanding this linear production. Instead of picturing a single line, it has become more of network or an environment, especially with global companies. This also means having good and effective communication with providers, suppliers, dealers, and franchises and providing modern tools and assets customized to promote collaboration and coordination. These could be B2B dynamic catalogs, providers' and distributors' portals, order management systems, and similar digital efforts.
3. On-demand is the new manufacturing dream
Having a great volume of stock products has been synonymous with global manufacturing companies. Warehouses, distribution centers, regional sites, and high-level logistics were needed to deliver goods around the world just to keep the cogs turning. This, however, has always carried big business risks: overproducing goods that needed an enormous salesforce to engage consumers, high investment before allocation of products, world-wide recalls for goods with faulty design and/or defects, and overall the slowness of companies to shift and respond to audiences with everchanging needs.
Drop shipping has been one of the methods that has helped retail companies to reduce stock (or rather depend on someone else’s stock), but it doesn’t really tackle the issues around overproduction. In reality, the big dream of the industry has formed around a demand-driven value chain. It is a business ecosystem that is agile and smart, powered by digital technologies, responsive to the demands of the end-user or clients, and capable of optimizing its processes with the information collected from IoT in everyday operations. By design, it responds to the principles essential to digital transformation we have reviewed before in this blog: connectivity, relevancy, information ad hoc, real-time communication and scalability, as well as visibility and enhanced management. Also important: in its more ideal implementation, it reduces the need for warehouses, logistics and other “wastes”, like lean manufacturing, and its principles have always preached.
4. When manufacturing becomes remote
Industrial equipment has evolved so much that remote manufacturing is now possible: operating machines from the other side of the globe using control dashboards with real-time monitoring, connectivity, and cloud-based systems. It certainly gives us a glimpse of a future with companies with decentralized operations. While it implies new levels of connectivity and security, the advantages are big: from avoiding downtimes in equipment (by allowing external scheduling) to putting expertise to the service of different sites (by allowing access to a team's knowledge and equipment for specific projects).
A naturally close ally for product innovation and R&D teams, remote manufacturing is on the rise as IoT keeps evolving. What is important to consider is that it operates through enterprise portals and dashboards, and as any modern business technology, it requires a digitally mature environment to thrive.
5. Knowledge produces the future
It is true that without information — such as reports, diagnostics and real-time monitoring of operations — you cannot tell what you are doing wrong in order to fix it in the next production cycle. It is a standard optimization process: looking at data, defining goals, targeting specific pain points, refining the process, and doing it better. Nowadays, the benefit has shifted to the future — it is with information that you can identify and avoid whatever you will be doing wrong in the coming days.
With the rise of advanced analytics and IoT, companies have become huge information producers. Artificial Intelligence and Big Data have allowed the industry to leverage their collected learnings to produce potential scenarios, prevent failures and downtimes, and envision the company’s operations in the future. With so many insights and sources of raw information, the need for good Information Architecture around business strategy is every day more important — channeling all this potential in a streamlined and easy to manage way through R&D portals, digital war-rooms, and knowledge hubs. These, on the other hand, will become the new battlegrounds for building roadmaps on new product innovation and tactical operations, as well as an overall guide for the company in every step of their (future) way.
Interested in applying these digital trends to your manufacturing company or a digital business environment? Get in touch with us. We love helping companies with their Digital Transformation journeys.